Deploying an AgBot into the field for the first
time is an exciting task. Efficiently and quickly gaining confidence in
operating it is crucial. Will every pre-defined obstacle be passed as prepared?
Will any random objects be detected and what if the AgBot has bad network
coverage? A couple of questions a farmer could ask during the early
relationship with his new ‘team member’. Within AgXeed, safety and reliability
are enablers in overcoming fears and building trust with the farmer. You
will therefore see a lot of safety solutions on the machines, but also beyond physical
safety measures, a lot is happening. Let’s investigate the details and see if
the AgBot can be as cautious as a farmer surveying the surroundings for a safe
work environment.
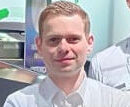
Pieter Rooijakkers
Sales & Product Trainer
The geo-fence system
Safety is incorporated from pre-planning to
execution, which means that before even setting up a task one of the most
important actions need to be performed. A well trained and certified person by
AgXeed must precisely survey the specific fields and fixed objects before it is
possible to send a task to the AgBot. The geo-fence acts as a safety boundary
for the AgBot and can never be crossed, not even with one millimeter. In that
case, we can make sure that the AgBot is not interfering with, for example
adjacent roads. In the AgXeed Cloud, it is possible to give certain users
specific rights, to ensure that misuse will be prevented.
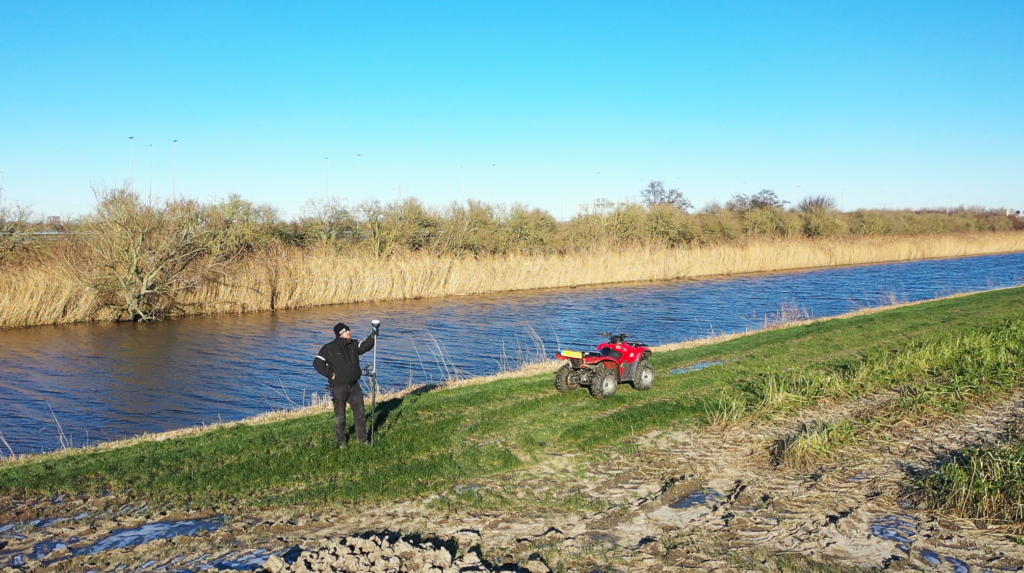
Safety functionalities
After calculating the task, safely attaching the implement(s) and transporting the AgBot to the field, the work can be started. During the start-up of the machine, several safety procedures take place before reaching full stability of every function. This not only includes checking if all emergency stops are functional, but also checking the insulation of the High Voltage wiring for example. When the safe state is reached, the machine is ready for work.
Within AgXeed, safety is considered as the number one priority. In addition to visual indicator lights and an audible alarm for warnings, the AgBot comes with emergency buttons situated both around the machine and on the remote control. Moreover, it is equipped with a comprehensive obstacle detection system comprising LiDAR, ultrasonic, radar, and contact-sensitive sensors to proactively avoid collisions.
Each mode or state is color-coded and visualized by LED lights on the machine. For example, when driving into the field boundary (geo-fence) the AgBot will tell you that it can now perform the task by showing a solid green light. When autonomy is started, a beeping sound can be heard, and the lights will change color. Furthermore, from the mobile App or in the AgXeed Cloud; it is possible to monitor the work. Not only camera footage can be inspected, but also sensor data and task process can be retrieved. When errors occur, logfiles will be available for further investigation. Besides monitoring the AgBot, the farmer can remotely pause and resume autonomy, but also to stop the engine in case of emergency.
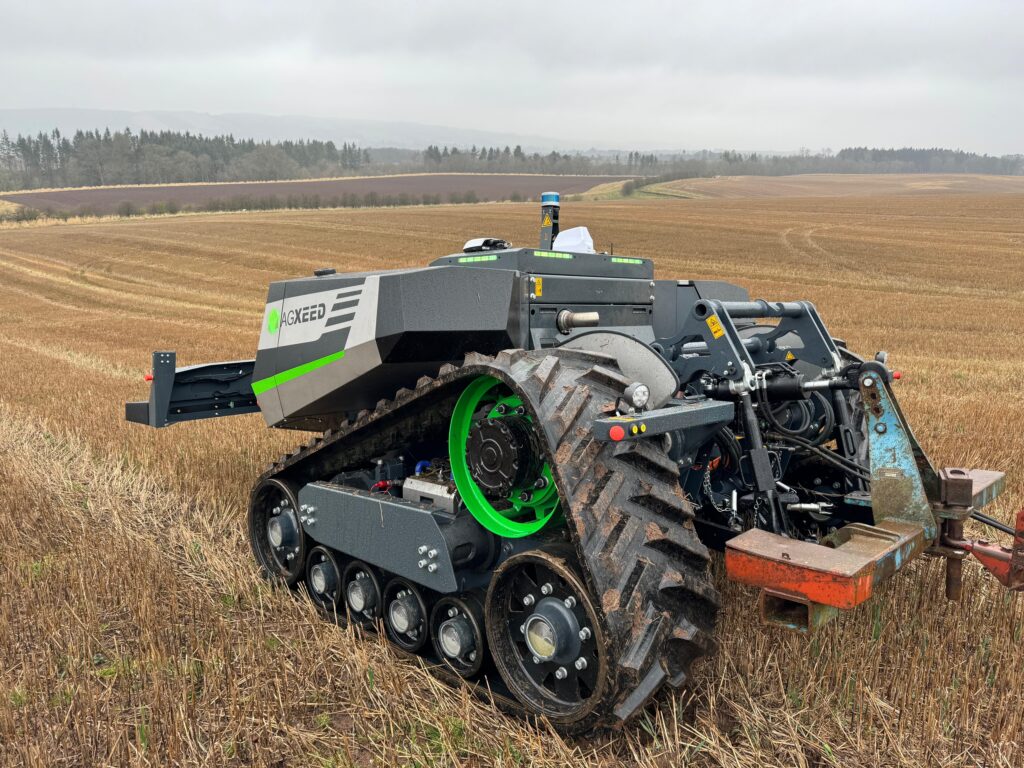
Green lights; the AgBot has entered the field boundary and can now deploy a task
Stopping
With the help of multiple physical safety sensors, the AgBot will be able to perform ‘soft’ and ‘hard’ stops in the field.
A hard stop for example occurs when an emergency stop is pressed, or the tactile sensitive bumper is touched. The engine will abruptly stall, and the park-brakes will be engaged, leading to an abrupt stop. To prevent this the
LiDar on top of the machine will detect objects from further away. A combination of object and vehicle motion will induce the machine to slow down and eventually stop if the object does not move. If the object moves within several seconds, the machine will continue on its own. If the object is fixed and not known by the AgBot, it will slowly come to a halt; engage its park-brake but not stall. The farmer will be notified and can then decide (from a distance) to continue or not.
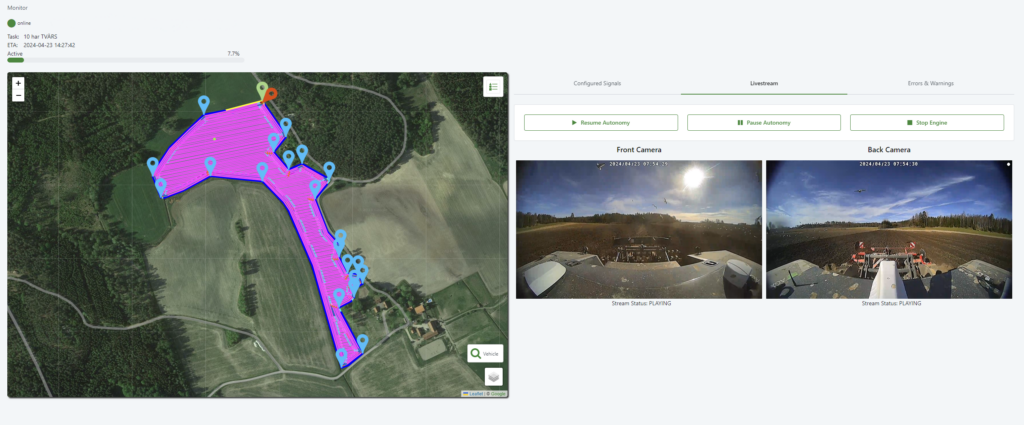
Safety features on and with the AgBot are all working
in redundancy which leads to high up-times and embedded protection. For
example, when internet connectivity is lost; the AgBot will keep track for 20
minutes without signal. Furthermore, the AgBot cannot operate autonomously
without the bumper; it lacks the necessary visibility and redundancy for
functionality.
Each element of the system contributes to
maintaining work safety and fostering trust among farmers globally. By
establishing a secure working environment, farmers can delegate tasks
confidently to the AgBot, allowing them to focus on other essential
responsibilities!